DOWNHOLE
AUTOMATION
The main contributor to risk and cost in deep drilling is the drill-string acting as a long spring. The AST will apply its algorithm downhole to automatically counteract and even out the axial and torsional slip cycles caused by the strong spring effect. The result is better drill-bit efficiency. The improved efficiency gives savings from at least three different sources:
Faster ROP, increased FOOTAGE and reduced equipment DAMAGE from less energy available to generate vibrations.
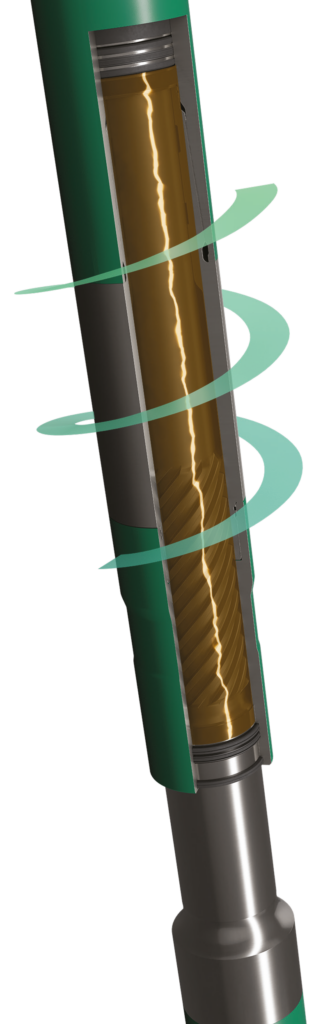
AST VALUE
The spring characteristics of the drill string will cause distortions to the delivery of power to the bit. It is easy to envision this by imagining what happens when the bit is lowered to bottom: the bit rotates steadily off bottom but will most likely stall as the cutters bite.
This is both because a gentle lowering of a long string is difficult, and also because the string conveys no torque at this point. With the cutters stuck in the rock, the torque needs time to build until the cutters slip and the bit turns.
Drilling science says that the severity of this stick-slip at the cutting interface is regulated by the axial compliance of the drilling system i.e. the freedom of the bit to move in the axial (up-down) direction. This way a BHA is capable of self-regulating stick-slip to a certain extent. Unfortunately, this also affects the loading of the cutters and limits the drilling efficiency.
The AST replaces the stick-slip mitigation from axial excitation through a dedicated mechanical regulator. This makes the stick-slip mitigation far more precise and provides for a significant improvement in drilling efficiency.
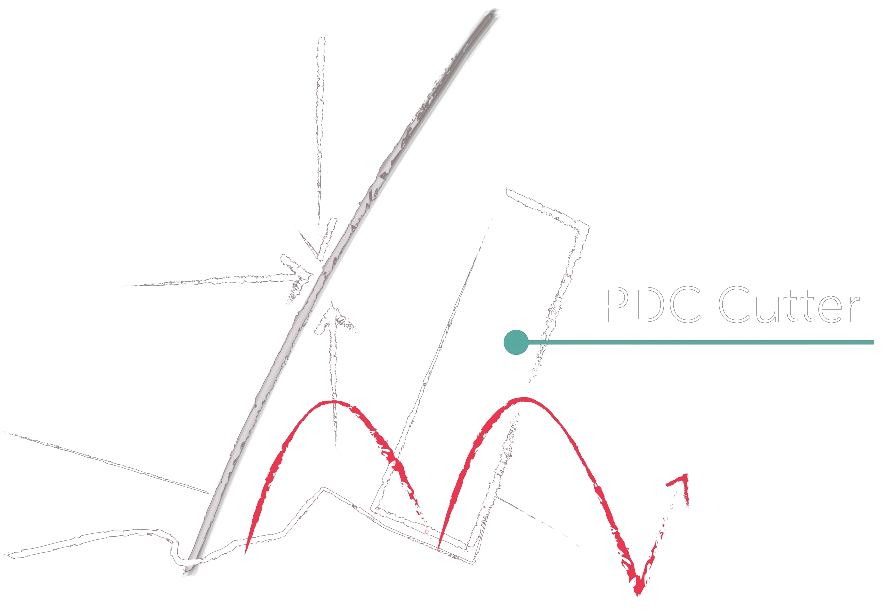
STIFF STRING
Axial excitation is how a PDC drill-bit solves overload in a conventional configuration
AST REGULATOR
The AST regulator adapts the load to the available torque. This happens in less than 30 milliseconds and provides for a steady cut
Few, if any vibration mitigation solutions have been through as many scientific tests as the Tomax AST. This picture is taken from the drillers chair on the IRIS, Ullrig in Stavanger. The tool is a 6 ” XC-AST with integrated recording of the motion and absorber pressures
DRILLSTRING
ISSUES
The long lasting PDC bits are perfect for deep drilling. However, things are different for the jointed pipe. Its flexibility becomes an increasing challenge as the well gets deeper.
The AST algorithm is designed to compensate for the instabilities induced by the long and flexible pipe. Our 6 3/4 inch OD XC-AST tool was used to drill the deepest well ever in 2022.
UK | 10 658 | BP May-97 |
Argentina | 11 184 | Total Mar-99 |
Qatar | 12 289 | Maersk/Qatar Petroleum May-08 |
Russia | 12 450 | ExxonNeftegaz Apr-13 |
Russia | 12 700 | ExxonNeftegaz Jun-13 |
Russia | 13 000 | ExxonNeftegaz Apr-14 |
Russia | 13 500 | ExxonNeftegaz Apr-15 |
Russia | 15 000 | ExxonNeftegaz Nov-17 |
UAE | 15 240 | ADNOC Oct-22 |
CASE EXAMPLE
MAINTAINING
A SHARP EDGE
IN HARD ROCK
In hard stringers, more force is required to engage the cutters. As a result, more heat is generated, thereby reducing the wear and impact resistance of PDC cutters. The inclusion of an AST tool in the BHA allows the use of more aggressive cutting structures to maximize drilling efficiency in terms of increased penetration rates and PDC durability.
The efficiency of a drill bit is generally determined by how sharp the cutter is. A sharp cutter requires less force to engage the rock and consequently creates less friction.
TIME-DEPTH CURVES
MAXIMUM BENEFIT
FROM PDC
Analysis of bit failures from modern drilling operations tends to reveal rock friction as a critical factor. In many cases, the compressive strength of the rock is less of a challenge compared to its coefficient
of friction. Friction in the drilling environment means heat and that is not good news for the Polycrystalline Diamond Compact (PDC) cutters. Neither does it go away with heavy set cutting structures.
The AST will greatly improve the benefit from PDC technology by allowing the use of more aggressive cutters that require less weight on bit. In addition to a reduction in vibrations, friction is reduced with less heat generated at the cutter interface, resulting in increased energy efficiency. Heat is the most important factor contributing to wear and impact resistance of PDC cutters.
NO STALLS WITH
DOWNHOLE MOTORS
With the AST positioned close to a drilling motor, any sudden reactive torque will cause the AST tool to immediately contract, reducing weight on bit and preventing the bit or mill from stalling. This function saves both time and equipment. Additional value is gained from reduced fatigue cycles in coiled tubing operations and a more controllable toolface orientation with steerable motors.
With an effective system for preventing stalls, the safety margin on the motor differential pressure can be lowered, enabling higher load limits with longer, more efficient runs.