New, counterforce assisted XC-AST Reveal Hard Rock Potential with PDC Bits
Objective
The cost of hard rock drilling grows exponentially with depth. That is not good news for geothermal projects. The exponent in the cost equation is the footage per bit. Tomax took on a full-scale test to find what could be done to PDC durability in basement rock by optimizing the balance in the rock-cutter interface.
FACTS
Tool
6 3/4” XC-AST
Country
Norway
Rig
Ullrigg
Section
8 ½”
BHA
PDC and AST
November 2015
Results
A 6 ¾” XC-AST tool was made up in the BHA with a new, API class M333 PDC bit from Halliburton DBS. On bottom, the energy to drill, or Mechanical Specific Energy (MSE), was continuously monitored to look for wear. It was evident that the bit would produce a steady cut with no axial impact loading. When speeding up by adding WOB, the MSE started indicating wear. The WOB was reduced and thanks to the self-sharpening effect of modern PDC cutters, the MSE recovered.
Value
Igneous rock generally has a high coefficient of friction. It became a valuable experience how heating and wear from friction was a big durability-barrier when the impact risk from the high compressive strength was solved.
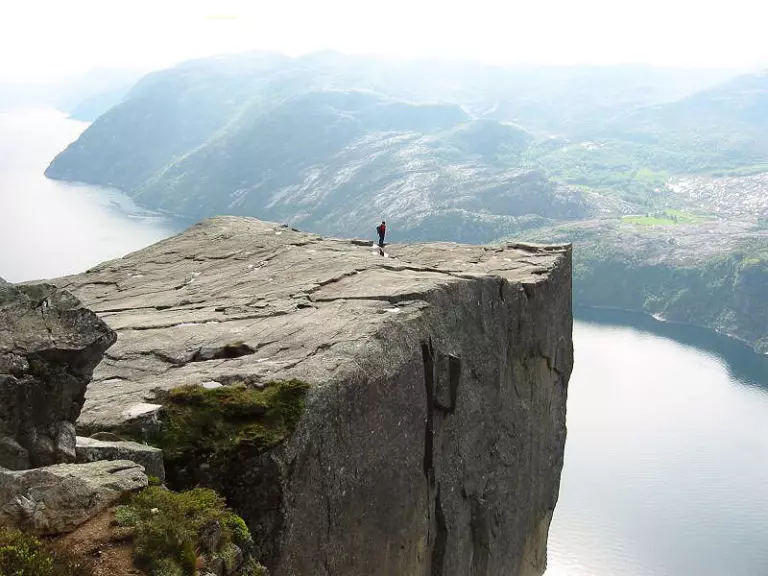
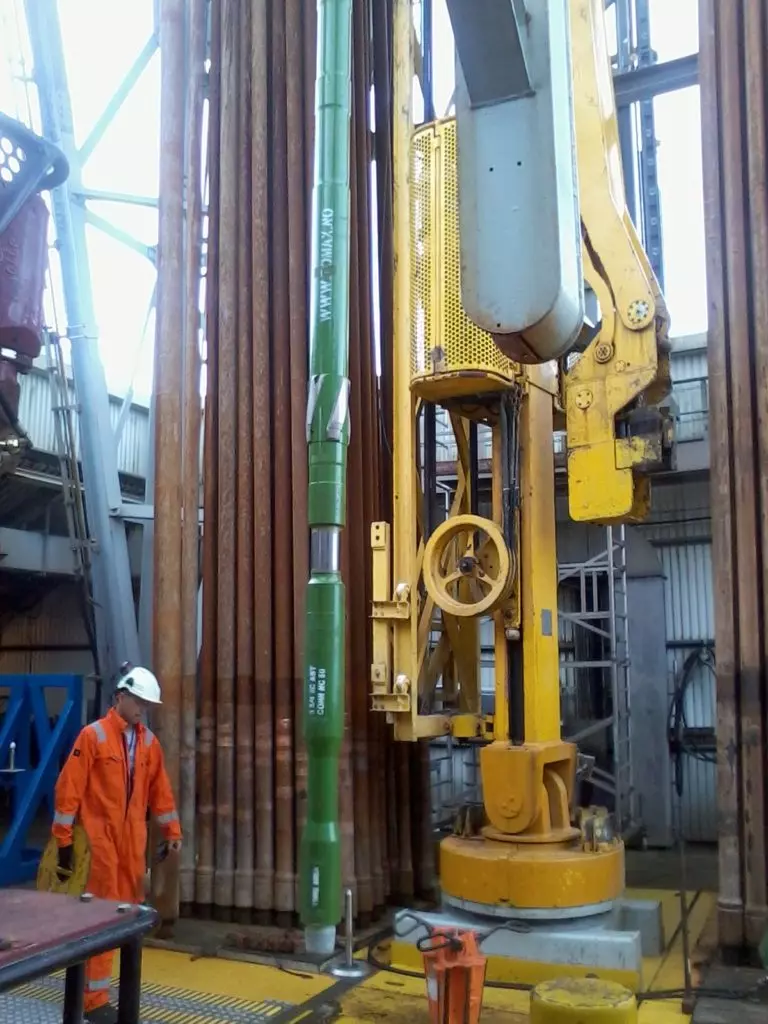